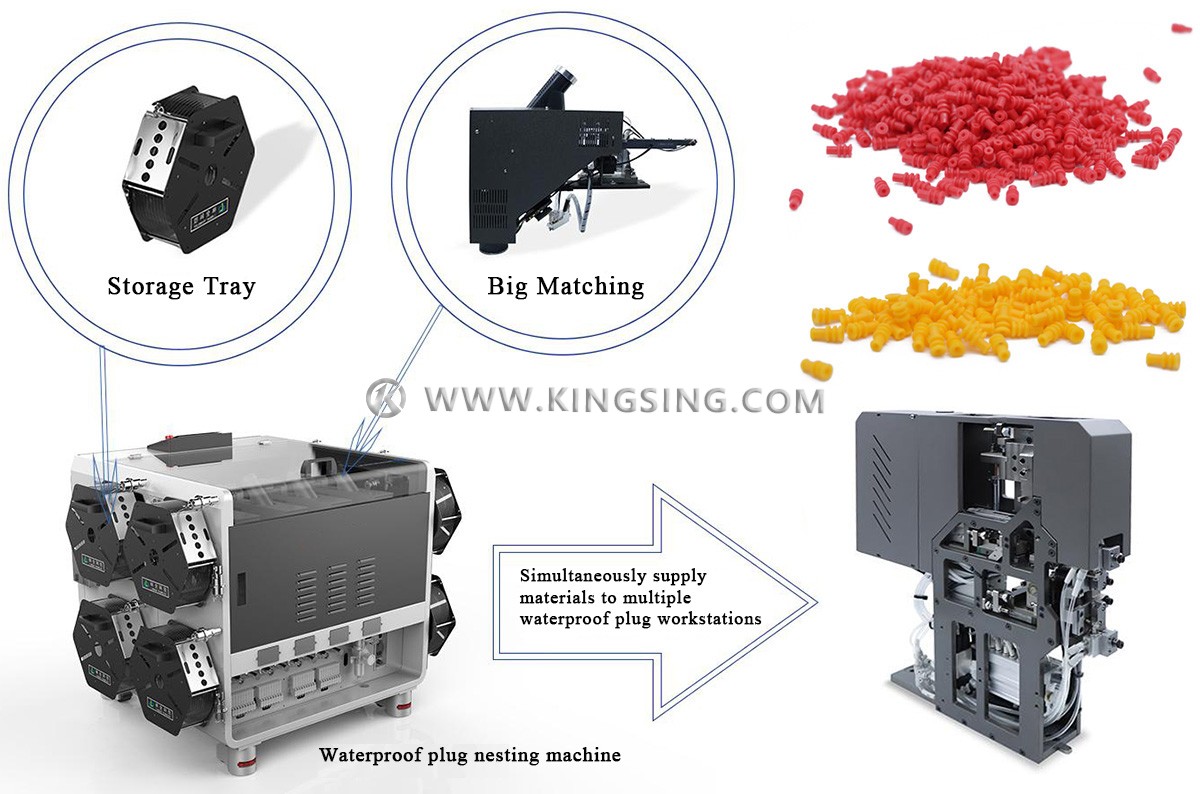
This production line is equipped with a waterproof plug discharge machine, which separates the waterproof plug feeding system from the piercing mechanism, and one feeding system can feed multiple waterproof plug piercing mechanisms at the same time. The machine automatically drives the waterproof plug into the storage tray first, and then mounts the storage tray to the station where the waterproof plug is inserted. It is extremely simple to replace the tray, and the material supply is more stable and reliable. The housing adopts the flow-type loading tray, and the double loading trays work alternately, so there is no need to stop the machine for manual loading. The terminal crimping machine is driven by a servo motor, and the crimping height can be set directly in the program without manually adjusting the screws. Multiple crimping stations can be selected arbitrarily in the program, and each type of wire supports crimping terminals on any station.
This machine adopts the concept of flexible design. One machine can process many different products. When replacing materials such as terminals, wires, housings, and waterproof plugs, you only need to simply replace the corresponding fixtures. After the current product is produced, there will be no idle waste of the machine, and it can be easily switched to produce other products. The program memory function can save the processing parameters of different products in the database. When switching products, the corresponding processing parameters can be called out with one key, saving debugging time.
Computer industrial control system, Windows operation interface, support network connection, can connect with local MES system through LAN, realize remote viewing of production data, remote production tasks and other functions. This machine also contains a full range of quality inspection tools, including terminal pressure monitors, CCD visual inspection systems, plastic shell pullout force sensors, terminal tension testers, terminal crimping height testers, etc., and the inspection data of each wire harness All are automatically saved to the database to achieve quality traceability management.
Applicable wire diameter: AWG26~11 (0.13~4.0mm2)
Cutting length: 200~9999mm
Cutting accuracy: ±(0.5+L*2‰) L=cutting length
Stripping length: ≤15mm
Wire selector: up to 50 different wires (can be customized)
Storage tray: 30 groups of storage positions
Number of shells: up to 30 housings can be inserted at one time
Housing feeding method: strip fixture or transfer tray (according to customer product selection)
Terminal machine output: 3T
Crimping Motor: Servo Motor
Number of terminal machines: 6 (3 or 12 can also be selected)
Insert waterproof plug station: 2 sets (other quantities can be customized)
Production efficiency: ≈1100 pieces/hour (insert plastic housings at both ends)
Operation interface: computer industrial computer, Windows system
Air pressure: 0.5~0.7Mpa
Rated power: 10KW
Working voltage: 380V 50Hz
Dimensions: 8019*1905*1775mm (take the model with 6 crimping stations as an example)
Detection device: CCD visual inspection, CFM terminal pressure monitor, pullout force detection, terminal tension tester, crimping height measuring instrument
Note:
The above specifications are for reference only. In the case of extremely hard, tough wires, processing may not be possible even within the cross section range. In case of doubt, KINGSING will be happy to provide processing samples of your wires.
Conforms to the relevant CE directives on machine safety and electromagnetic compatibility.